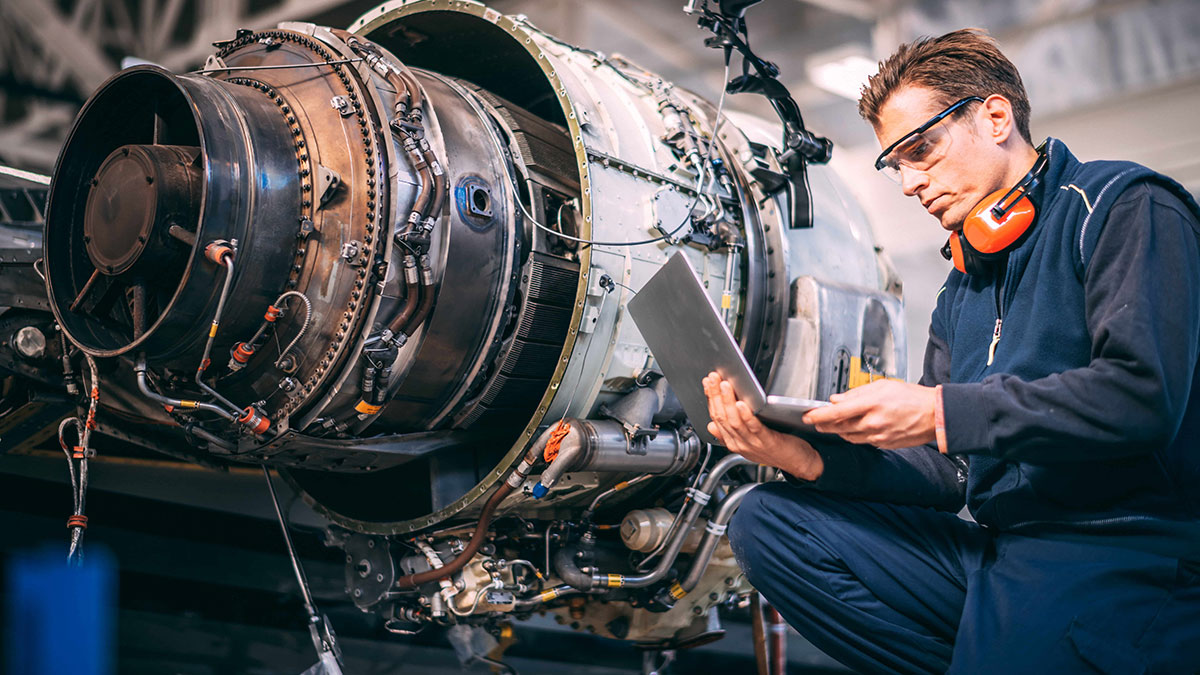
Das Potenzial von Maschinendaten nutzen
Zurück zum BlogIn der Druckerei herrscht reger Betrieb: Es werden tausende Broschüren gedruckt, Druckfarben nachgefüllt, Papier zur Verarbeitung bereitgestellt, Druckerzeugnisse zum Versand gebracht. Künstliche Intelligenz optimiert dabei die Produktion durch die Analyse von Maschinendaten.
6 Millisekunden früher kommen die Druckbögen aus der Maschine. Für Menschen weniger als ein Wimpernschlag, für Druckmaschinen jedoch eine magische Grenze, bei der eine Reinigung ihrer Transporträder notwendig wird. Nur künstliche Intelligenz registriert diesen kaum wahrnehmbaren Unterschied und kann diese Information verarbeiten. Erst KI-Technologien entlocken den Log-Files von Maschinen wertvolle Informationen, revolutionieren die Wartung und Reparatur und läuten das Zeitalter von Industrial Intelligence ein.
Denn das KI-basierte System für die Maschinenüberwachung hat bereits prognostiziert, dass die Papiertransporträder langsam verschmutzen und spätestens nach dem Druck von weiteren 200.000 Bögen gereinigt werden müssen. Der Fertigungsleiter ist darauf vorbereitet und plant seine Produktion entsprechend, um den Auftrag pünktlich fertig zu bekommen.
Industrial Analytics optimiert mehr als nur Maschinenverfügbarkeit
Was nach einem ganz normalen Tag in einer Druckerei aussieht, ist die nächste Entwicklungsstufe der Industrie 4.0: Industrial Analytics. Eine Disziplin, die es sich zur Aufgabe gemacht hat, das immense Potenzial von Maschinendaten für die Optimierung von Wartungs- und Produktionsprozessen nutzbar zu machen.
Die Analyse von Maschinen- und Prozessdaten ist nichts Neues und bei kritischen Anlagen bereits seit Jahrzehnten üblich. Doch die Einleitung von entsprechenden Maßnahmen erfolgt häufig erst reaktiv, da die Logs zunächst ausgelesen und dann offline analysiert werden. Ein Handlungsbedarf wird im schlimmsten Fall erst dann erkannt, wenn bereits ein gravierendes Problem besteht. Auf diese Weise ist es nicht möglich, einen weltweiten Maschinenbestand kontinuierlich zu überwachen und proaktiv zu handeln.
Das hat sich dank den heutigen KI-Verfahren grundlegend geändert: Sensor-, Log-, Prozess- und Produktionsdaten werden durch digitale, automatisierte Analyseprozesse erfasst und performant in der Cloud verarbeitet. Auf diese Weise können Informationen über die Anlage in Echtzeit ausgewertet werden.
Ein solcher Ansatz ist skalierbar und eine wichtige Voraussetzung, wenn es darum geht, vorausschauenden Service für mehrere tausend Maschinen oder Anlagen weltweit zu leisten. Die neuen Möglichkeiten zur Auswertung der Datenbasis ist aber nur der erste Schritt, um Erkenntnisse für die Produktion, Wartung und Weiterentwicklung der Produkte ziehen.
Vom Asset zur Aktion – und zurück
Neben den richtigen Algorithmen und der performanten Auswertung ist es genauso wichtig, die Nutzung der Informationen und Erkenntnisse im Unternehmen zu steuern. Der nächste Schritt zur Industrie 4.0 kommt also um die Systemintegration nicht herum, um dank der Vorhersagen proaktiv Wartungsmaßnahmen einzuleiten oder neue Erkenntnisse zur kontinuierlichen Optimierung der Maschinenleistung zu verwenden. Durch die Anbindung von Ticketing-Systemen lassen sich bspw. automatisiert neue Tickets anlegen, sobald kritische Werte überschritten wurden. Genauso können dank moderner KI-Verfahren ja nach betroffenem Bauteil die entsprechenden Montage- und Wartungsanleitungen direkt an den Servicetechniker gesendet werden.
Dabei bleibt die Systemintegration keine Einbahnstraße, denn es muss auch sichergestellt werden, dass Informationen über tatsächlich durchgeführte Maßnahmen und dabei gewonnene Erkenntnisse in die Fallbetrachtung kontinuierlich zurückfließen und so ein Kreislauf aus Lernen und Verbessern entsteht.
Die Fragen gehen dabei ins Detail:
In wie vielen Fällen war die Prädiktion richtig?
Welche weiteren Analysen von Log-Daten sind relevant?
Welcher Produkttyp zeigt die Fehler am häufigsten?
Könnte ein Serienfehler vorliegen?
Digitale Transformation im Service
Die Entwicklung solch integrierter Systeme in der Fertigungsindustrie ist aber kein Selbstzweck und geht weit über das Ziel einer höheren Maschinenverfügbarkeit hinaus. Denn neben der Instandhaltung wird das Potenzial der Daten für die Produktionsoptimierung von vielen Unternehmen häufig übersehen.
Stattdessen arbeiten sie manuell mit Listen und Excel-Tabellen und verlassen sich auf das Wissen einzelner Experten – im Angesicht des demografischen Wandels ein riskantes Unterfangen. Eigentlich schade, denn mit der Datenanalyse ließe sich so viel mehr anstellen und neuer Umsatz generieren, indem bspw. eine Wartungsplanung auf Basis der Maschinendaten als neuer Service angeboten wird, der Ausfälle proaktiv verhindert und die passenden Ersatzteile gleich mit anbietet.
Von solchen Modellen profitieren Anbieter und Kunden gleichermaßen: Ein verbesserter Betrieb sichert Produktionskapazitäten, während Informationen über die tatsächlich durchgeführten Wartungs- und Reparaturmaßnahmen das System immer präziser in seinen Vorhersagen macht.
Darüber hinaus lassen sich aus Betreibersicht Erkenntnisse für die Gesamtanlageneffektivität GAE (engl. OEE) gewinnen. Um hier Optimierungen vorzunehmen, muss aber der gesamte Prozess hinsichtlich den drei Kernfaktoren Anlagenverfügbarkeit, Produktivität und Qualität zusammenhängend analysiert werden und ständig an sich verändernde externe Einflussfaktoren, wie etwa schwankende Rohstoffqualität, angepasst werden. Aufgrund der hohen Komplexität und des Datenvolumens ist es an der Zeit, für die Optimierung der Vorgänge die Erfahrungen einzelner Mitarbeiter mit einer KI-basierten Datenanalyse zu erweitern. Nur so erhält man die Chance zur Objektivierung und systematischen Verbesserung.
Industrial Analytics legt deshalb den Fokus auf den Geschäftswert der Daten, nicht nur auf die Analyse selbst. Es geht nicht um die Algorithmen, sondern darum, dass Betreiber ihre Maschinen, Geräte und Prozesse verstehen: Wie funktionieren sie wirklich? Wie können diese messbar gemacht werden? Und wie kann deren Verhalten vorhergesagt werden? Somit begleitet Industrial Analytics den gesamten Prozess: Von der Datenanalyse bis zur richtigen Maßnahme. Unternehmen können so ihr Ersatzteil- und Betriebsmittelgeschäft optimieren, neue datengetriebene Geschäftsmodelle entwickeln und ihr Leistungsangebot im Service erweitern.