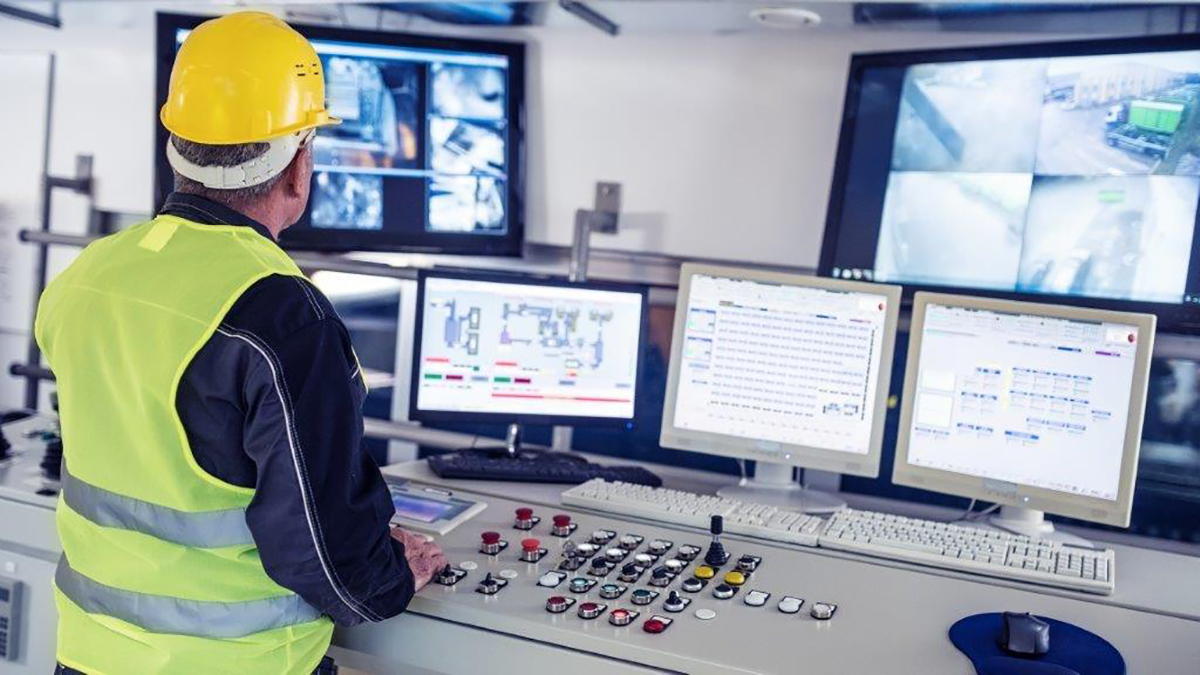
Industrial Analytics ist keine Magie!
Zurück zum BlogIndustrial Analytics erfasst und analysiert in Echtzeit die Daten- und Sensorströme von Maschinen und Anlagen. Durch intelligente Technologien lässt sich anhand von Zeitreihendaten exakt berechnen, wann z. B. der Verschleiß einer Maschine so hoch ist, dass bestimmte Komponenten ausgetauscht werden müssen.
Durch die intelligente Vernetzung von Maschinen entlang der gesamten Produktionskette werden in der Fertigungsindustrie immer größere Datenmengen produziert, das sogenannte „Industrial Big Data“. Industrial Big Data ist im Zuge das Internets der Dinge bzw. Industrie 4.0 entstanden und umfasst, in Abgrenzung zu „herkömmlichem“ Big Data, primär Daten, die von Maschinen- und Anlagen produziert werden. Diese sind in ihrer Menge nicht nur unüberschaubar groß, sondern auch völlig heterogen: Temperaturmessungen, Stromverbrauch und Druck in der industriellen Fertigung, Leistungsdaten von Motoren, Log-Dateien von Fertigungskomponenten zu anderen Maschinen in der Prozesskette oder Umgebungsdaten von Maschinen wie Luftfeuchtigkeit und Raumtemperatur.
Für Unternehmen bergen diese Daten ein immenses Potenzial zur Optimierung der eigenen Produktionsprozesse und Wartung. Um dieses heben zu können, müssen die Maschinendaten analysier- und auswertbar gemacht werden. Und hier kommt Industrial Analytics ins Spiel!
Industrial Analytics und Predictive Maintenance gehen Hand in Hand
Industrial Analytics erfasst und analysiert in Echtzeit die Daten- und Sensorströme von Maschinen und Anlagen. Durch intelligente Technologien lässt sich anhand von Zeitreihendaten exakt berechnen, wann z. B. der Verschleiß einer Maschine so hoch ist, dass bestimmte Komponenten ausgetauscht werden müssen. Damit können Vorhersagen zu Ausfällen oder Problemen von Maschinen- und Anlagenteilen getroffen und Predictive Maintenance betrieben werden.
Predictive Maintenance bedeutet nichts anderes als die vorausschauende Wartung von Maschinen, Motoren, Anlagen, Geräte oder Komponenten. Mithilfe von Predictive Maintenance können Hersteller, Betreiber oder Techniker frühzeitig Wartungsmaßnahmen einleiten oder rechtzeitig Ersatzteile bestellen, um Stillstände oder Ausfälle von Maschinen oder Anlagen zu vermeiden. Dies reduziert die Kosten in der Instandhaltung drastisch und verbessert gleichzeitig den Service nachhaltig.
Neben Predictive Maintenance lässt sich mit Industrial Analytics auch die Effektivität von Produktionsprozessen beurteilen oder Produktionsprozesse durch die Identifizierung von Fehlerquellen optimieren.
Anhand von Industrial Analytics und der systematischen Datenanalyse erhalten Betreiber und Hersteller valide Entscheidungsgrundlagen zur Optimierung von Fertigungsprozessen und können so ihre Produktivität steigern und sich Marktvorteile verschaffen.
Damit Industrial Analytics erfolgreich eingesetzt werden kann, ist die richtige Frage entscheidend: Was möchte man herausfinden? Was ist die Ursache eines Problems? Wie dringend muss es beseitigt werden? Welche Ersatzteile werden benötigt?
Die richtigen Fragen sind viel wichtiger als Algorithmen.
Um die richtigen Fragen stellen zu können, müssen die zu untersuchenden Maschinen, Geräte und Komponenten und deren Prozesse verstanden werden. Erst dann kann man die geeignete Analysemethode und die entsprechenden Algorithmen auswählen.
Nehmen wir als Beispiel den Bruch eines Auslassventils eines Dieselmotors. Daraus resultieren schwerwiegende Folgeschäden für den Motor, u. a. Zerstörung des Zylinderkopfes und schließlich des Turboladers.
Dieser Schaden lässt sich mithilfe von Industrial Analytics vorhersehen und verhindern. Dafür ist ein grundlegendes Verständnis notwendig, welche Rolle das Ventil im Verbrennungsprozess spielt: Ist das Ventil beschädigt, jedoch nicht zerstört, kann es die Verbrennungskammer nicht mehr perfekt abdichten. Infolgedessen ist der Verbrennungsprozess weniger effizient.
Dieser verschlechterte Wirkungsgrad zeigt sich in einer sinkenden Abgastemperatur. Die gute Nachricht ist bei modernen Motoren: Die Abgastemperatur wird von Sensoren gemessen, d. h. diese Daten sind stets aktuell verfügbar und können für die Problemerkennung herangezogen werden.
Somit lässt sich die Prämisse für die Datenanalyse bestimmen: Die Feststellung einer Abweichung der Abgastemperatur. Die klare Formulierung des Problems macht es letztendlich leicht, den dafür geeigneten Algorithmus auszuwählen.
Dazu wird eine mathematische Funktion zur Bestimmung der erwarteten normalen Abgastemperatur benötigt. Es gibt hierfür auch Simulationsmodelle für derartige Berechnungen, jedoch erfordern diese die experimentelle quantitative Bestimmung physikalischer Prozesskonstanten. Dies ist in der Praxis viel zu teuer und zu aufwendig. Deshalb werden die Daten des tatsächlichen Prozesses im Motor herangezogen.
Im Rahmen der Simulation bilden die Konstanten die individuellen Eigenschaften eines bestimmten Motors ab. In den aktuellen Daten der variablen Parameter eines Motors sind diese Informationen implizit enthalten. Die Bereinigung des Simulationsmodells resultiert in einem vereinfachten empirischen prädiktiven Modell für die Schätzung der erwarteten Abgastemperatur des Motors.
Die Eingabeparameter sind u. a. die Ladelufttemperatur, die Motordrehzahl, die produzierte Abgabeenergie und die Temperatur der Umgebung. Letztere muss den Temperaturveränderungen nachts und tagsüber standhalten. All diese Daten liefert das Motorüberwachungssystem.
Für eine vollständige Analyse sind noch weitere Metadaten notwendig:
Gerätemetadaten – Typ, Baujahr etc.
Sensor- und Nachrichtenmetadaten – hierbei gilt es zu beachten: Ein Temperatursensor einer amerikanischen Maschine gibt seine Messungen ggf. in Fahrenheit an, während eine deutsche Version dies in Celsius tut. Oft wird der gleiche Fehler anhand verschiedener Fehlercodes gemeldet, was vom Herstellungsjahr und/oder unterschiedlichen Firmware-Versionen abhängig ist. Somit ermöglichen Sensor- und Nachrichtenmetadaten die Normalisierung und Vereinheitlichung der Messdaten.
Geschäftsmetadaten – je nach Wartungsgeschäftsmodell bestehen für verschiedene Maschinenbediener oder -eigentümer unterschiedliche Wartungsverträge, z. B. die unterschiedliche Verfügbarkeit von Diensten zur Fernüberwachung und -meldung. Diese Informationen müssen ebenfalls bei bestimmten Geräten berücksichtigt werden.
Zusammenfassend sind die Voraussetzungen für den erfolgreichen Einsatz von Industrial Analytics:
Verstehen von Ursache und Wirkung
Ermittlung eines geeigneten prädiktiven Modells (die Vorhersage normaler Werte ermöglicht die Erkennung abnormaler Werte)
Verfügbarkeit der erforderlichen Eingangsdaten
Auswahl und Anwendung des geeigneten Algorithmus